Is That Dress Printed?: The Benefits and Uses of 3D Printing in Fashion
- Nour Tahan
- Oct 22, 2022
- 4 min read
Updated: Nov 20, 2022
Nour Tahan. October 22, 2022
Since its invention, three-dimensional (3D) printing has been widely utilized in a variety of industrial economies, including the medical and transportation industries. It has also progressively gained popularity with Computer Aided Design (CAD) enthusiasts who can now buy and use a 3D printer at home (Sun, D & Valtas, 2016).
The technology of 3D printing makes it possible to avoid some of the drawbacks of traditional production, one of which is the lack of flexibility. It should be emphasized that since the entire unit was constructed individually, changes to meet improvements or changes in fashion could be made with ease. The production preparation procedure is also straightforward since it requires fewer phases. Because the size, colour, and form of the created 3D item can be quickly altered on a computer without incurring additional costs, it is useful for both mass manufacturing and making prototypes or samples on a small scale (Sun, D & Valtas, 2016).
Research centres throughout the world are concentrating on ways to improve the process' performance in terms of speed or material qualities. This is essential, but this part also discusses very effective business models that have previously been accomplished by recognizing the advantages of 3D printing and selecting the right applications. Some of the primary advantages that any 3D printing method offers are so large that they easily surpass any possible negatives, even in the absence of the best material or process performance (Karel Brans, 2013).
It is now feasible to produce single lot sizes at reasonable prices because traditional machining and tooling are not necessary. Complexity comes without cost. There is no additional expense for a much increased geometrical complexity, which is a striking contrast to traditional machining. As seen in the topology-optimized chair in Figure 2, the complex features can serve a variety of purposes, such as padding (Karel Brans, 2013).
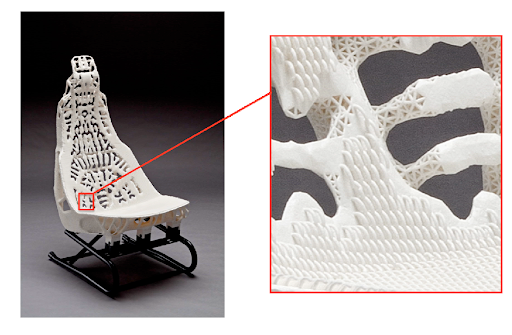
Fig.1. Complex lightweight design, enabled by 3D Printing
as presented by A. Kawamoto (Toyota) in 2012)
3D item printing may be done in a single setting; cut time is determined not only by manufacturing but also by assembly. This leads to the understanding that if fewer parts need to be created, waste can be decreased. The garment manufacturing business would benefit greatly from this, as fabric waste is one of the main problems when mass producing brands without taking into account things like cutting seam allowances, altering pattern size, altering pattern lay plans, and many other things. Zero material waste will be achievable if it is possible to completely remove the cutting process since 50% of the final cost of a garment is made up by the cost of the material that has been used in production (Sun, D & Valtas, 2016).
The types of materials that can be utilized in 3D printing have increased as a result of new market advances that have increased the types of materials from which filaments may be created. In fact, filaments may be produced from a variety of materials, including metals, ceramics, cotton, and numerous types of plastic (including a form of nylon).
For instance, Continuum, a California-based start-up fashion firm, sells a 3D-printed bikini made from nylon plastic filament. Nike has also experimented with filaments in the creation of their Laser Talon sneakers (Jeanette Cuzella, 2015).
Other researchers have explored 3D printing clothing, but not using fabric, therefore no standard for seam building approach has been given. Initially, it was planned to stitch the pieces together, however it was discovered during testing that the printed panel texture would prevent this from happening. Instead, it was decided to smooth the fabric seam edges and melt the 3D-printed textile onto the fabric, which has been shown to be a far more visually pleasing method of seam building. In the clothing industry, this type of seam construction method was utilized (Sun, D & Valtas, 2016).
The front, shoulder, and back are the three primary components of the printed garment section, and they are printed in both their original and mirror dimensions. Figure 2a shows the front panel of the print, which uses 26.98 grammes of polymer and takes 2 hours, 12 minutes to print, the shoulder panel, which uses 16.45 grammes of filament and takes 1 hour, 25 minutes, and the rear panel, which uses 30.24 grammes and takes 2 hours, 33 minutes (Figure 2c). The entire material consumption of the top half of the dress is 147.34 grams, and the total print time is 12 hours 36 minutes, with a material cost of £8.70 (Sun, D & Valtas, 2016).
Fig 2a Fig 2b Fig 2c

(Fig.3: Whole garment with the top part made by 3D printing.)
References
Brans, K. (2013, June 11). 3D printing, a maturing technology. IFAC Proceedings Volumes. Retrieved November 19, 2022, from https://www.sciencedirect.com/science/article/pii/S1474667015357190
Cuzelle, J. (2015, April 6). A PROPOSAL FOR COPYRIGHT PROTECTION OF 3D-PRINTED APPAREL. Retrieved November 20, 2022, from https://ctlj.colorado.edu/wp-content/uploads/2015/08/Cuzella-final.pdf
Sun, D & Valtas, A 2016, '3D Printing for Garments Production: An Exploratory Study', Journal of Fashion Technology and Textile Engineering, vol. 4, no. 3, 1000139. https://doi.org/10.4172/2329-9568.1000139
Comments